Top Guidelines Of Indonesia Furniture Manufacturers
Wiki Article
How Indonesia Furniture Manufacturers can Save You Time, Stress, and Money.
Table of ContentsExamine This Report on Indonesia Furniture ManufacturersIndonesia Furniture Manufacturers Fundamentals ExplainedIndonesia Furniture Manufacturers for DummiesIndonesia Furniture Manufacturers Fundamentals ExplainedThe smart Trick of Indonesia Furniture Manufacturers That Nobody is Talking About
Nonetheless, there are some disadvantages to buying from a furniture producer. For one, you might need to wait longer to receive your furniture considering that it's being made to order. Additionally, you may not be able to see or touch the product before you get it. A furnishings merchant is a business that offers furniture made by different makers.When you purchase from a furniture retailer, you're buying a furniture piece that's already been made and prepares to be shipped to your home. Among the advantages of purchasing from a furniture store is that you can often see and touch the item prior to you purchase it.
At BH Furniture, we think in establishing new criteria for excellence in the production of business furniture - Indonesia furniture manufacturers. Our commitment to innovation has actually led us to accept advanced automation technology, changing the method we manufacture furnishings and pushing us to the forefront of the sector. Gone are the days of manual work controling the manufacturing floor
Say farewell to manufacturing hold-ups and overtime prices. This implies we not just fulfill but surpass distribution deadlines, offering our customers with a degree of integrity that typical manufacturing approaches merely can not match.
Examine This Report on Indonesia Furniture Manufacturers
Our production capacity has actually skyrocketed, allowing us to fulfill the needs of even the largest tasks without endangering on high quality. As your partner in commercial furnishings options, we can easily scale our outcome to fit your requirements, no issue the scale. While traditional production relies greatly on hand-operated labor, our automated systems have actually dramatically reduced our dependence on a big labor force.Furniture manufacturing is a complex procedure that includes different phases, from designing and product option to manufacturing and setting up. At each phase, there is an opportunity of problems or errors that can endanger the high quality of the final item. To make sure that furnishings is of top quality, furnishings makers carry out high quality control processes to determine and correct any kind of issues that might develop during manufacturing.
The assessment process should cover numerous elements, such as setting up, finish, colour, style, product packaging, labelling, and marking. By carrying out a rigorous evaluation procedure, producers can guarantee their items meet the required top quality, safety, and toughness needs. They also offer the adaptability to address issues and make adjustments prior to finishing the last product.
Furnishings quality standards are sets of guidelines and demands for furniture production. They specify the required quality level of furnishings manufacturing and cover aspects such as safety, longevity, stamina, and ecological influence.
The Single Strategy To Use For Indonesia Furniture Manufacturers

To guarantee their furniture items can endure different weather aspects, consisting of sun, rainfall, snow, and wind, manufacturers need to consider worldwide recognized criteria that make up inspections and testing. Below are some of the criteria to keep in mind: ASTM F1561-03 is a global basic established by the American Area of the International Association for Testing Materials (ASTM).
UL 962 is a worldwide safety and security continue reading this standard established by Underwriters Laboratories (UL), an independent global supply safety services company. The conventional uses to family and business home furnishings, consisting of outside furnishings.

More About Indonesia Furniture Manufacturers
It helps to determine flaws in the furniture and evaluate its performance and compliance with the called for high quality criteria. Here are the actions for performing laboratory screening for furniture: Producers collect samples of furniture components that require screening. These samples generally stand for the different kinds of furniture that they generate.This may entail a mix of various examinations, including stamina testing, sturdiness testing, security testing, and environmental influence screening. The samples are then examined for numerous high quality specifications, such as strength, durability, safety and security, and ecological influence. The outcomes are then evaluated to determine whether the items fulfill the called for top quality criteria.
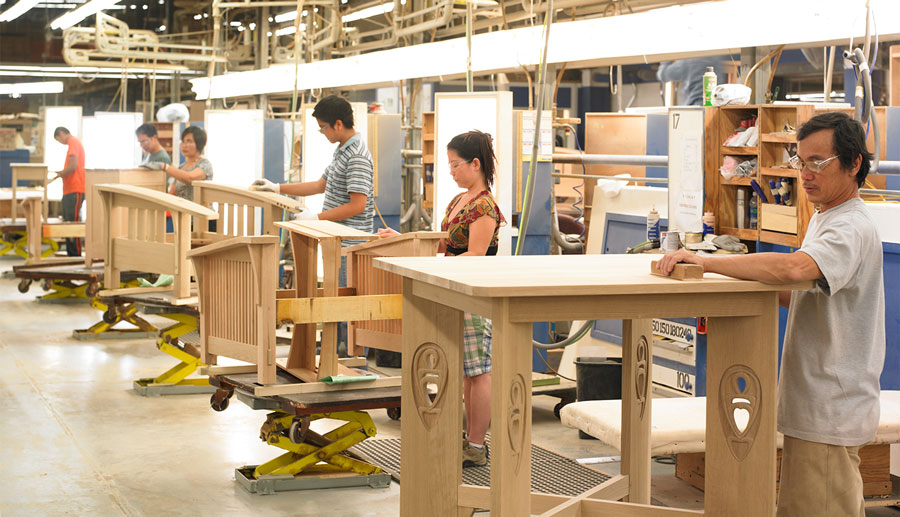
Generally, every retail shop furniture is i loved this various. Layouts conference consumer comfort Making the most of space usage in storage space, display screen, tramp, visitor seating and walkways Guaranteeing convenience of accessibility to items for trials and purchase Creating modular furnishings that is simple to move and refit Meeting safety and security demands of clients A quick TAT from design to production and installment with very little errors can help resolve the above problems.
What Does Indonesia Furniture Manufacturers Mean?
Likewise, a developer can understand the market trends and be all set with cutting-edge styles in advance. Read below: Exactly How DriveWorks Aids You to Lower Preparation in Manufacturing Developers typically need to change the sizes and shapes of furniture at a minute's notification. These may have different visual and functional demands like front workdesk, and servicing workdesk that differ in dimensions.Boosts product top quality and minimizes scrap. Field guideline files along with amount takeoffs are additionally produced for retail store furniture installations. Design models and conflicts are minimized, this contact form and the shop floor can begin manufacturing on the day of sales.
It is a highly competitive market, with services making every effort to maintain up with changing consumer needs and the most recent technical trends. Today's consumers are much more likely to prefer furnishings that is tailored and made with lasting products.
Report this wiki page